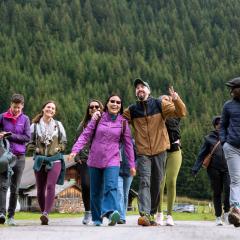
Developing an Autonomous Cargo Boat for Medical Deliveries
December 5th, 2017
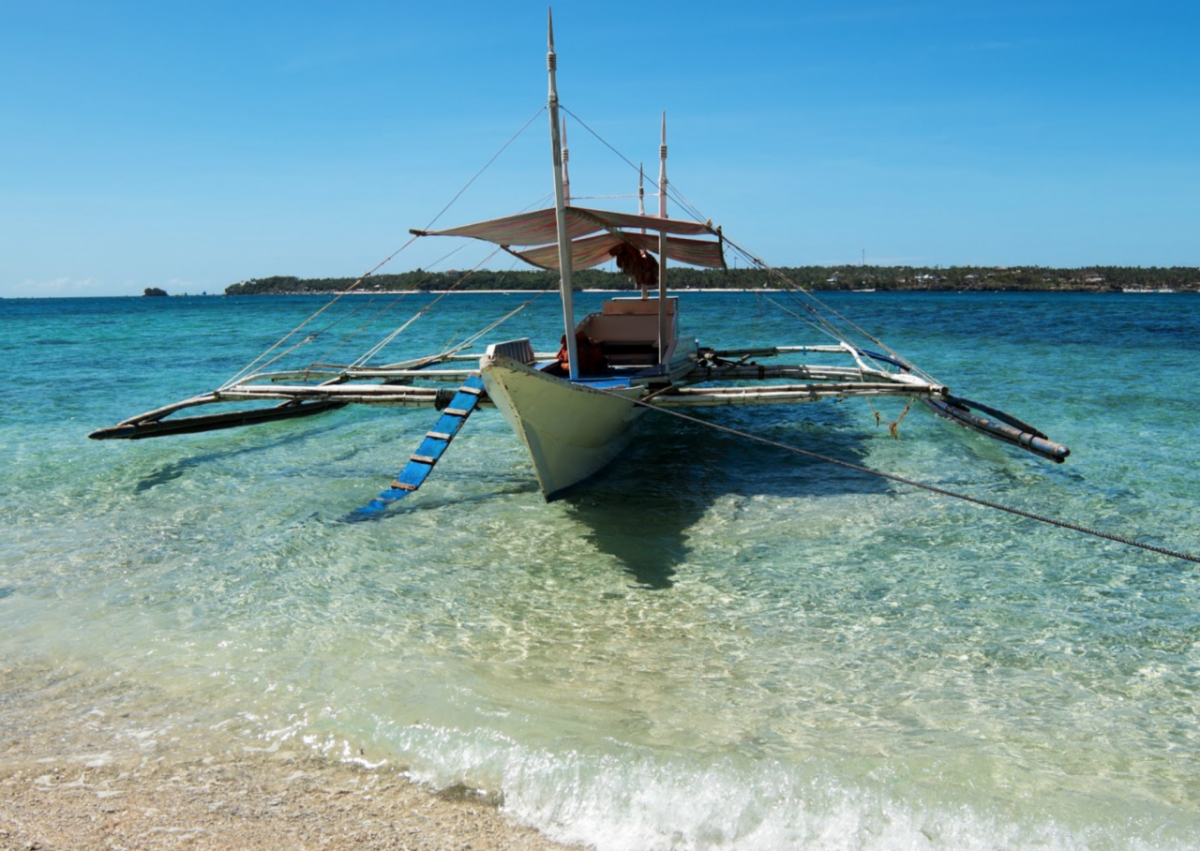
"We’d love to do a robotics project with a humanitarian focus. Several of us work in Dr. Vijay Kumar’s robotics lab at UPenn and have experience with aerial and ground based robots." So read an email I received from a team of 6 enterprising students from the University of Pennsylvania (UPenn). Dr. Kumar is the Dean of the Engineering Department at the University of Pennsylvania and sits on the Board of WeRobotics, hence the connection to UPenn. The guest blog post below on our joint project with UPenn was kindly written by the students leading this collaboration: Nadia Kreciglowa, Anurag Makineni, Thomas Mulroy, Shreetej Reddy, George Sun and Brian Zhang (in alphabetical order). We're thrilled to be working with each of them and grateful for their hard work, commitment and camaraderie.
Introduction
We’re a group of six students at the University of Pennsylvania studying mechanical engineering who are passionate about humanitarian robotics. After reading this on the WeRobotics blog about applications of autonomous maritime vehicles, we decided to work with the WeRobotics team to develop a solution for small-scale medicine delivery in the Philippines. Our goal is to develop an autonomous surface vessel that is easy-to-deploy, reliable, and affordable.
Background
The Philippines is a nation comprised of 7,641 islands, of which around 2,000 are inhabited. These islands range in size and population, from under a square kilometer to over 100,000 km, and from several hundred inhabitants to over 50 million. On many smaller, outlying islands, residents continue to have difficulty accessing essential medicines. Few medical centers have been built on these islands, largely due to inadequate infrastructure to transport such medicines. The centers that have been built have access to only around 20% of the medicines they require. The current infrastructure, comprised primarily of large ferries and outrigger canoes, is infrequent, unreliable, and expensive. One of the regions with this problem is the Cuyo Archipelago, which is the focus of this project.
Figure 1: Commonly used outrigger canoe.
Figure 2: The Cuyo Archipelago’s location in the Philippines.
The Cuyo Archipelago is located south of Manila in the Sulu Sea in the Palawan region. The archipelago comprises 45 islands and is inhabited by over 45,000 people. Cuyo Island, the largest island in the archipelago, is home to around half of the archipelago's residents. While Cuyo Island has access to an airport, hospital, and medical supplies, the half of the archipelago's population in the other isles has less available access to medical care.
This medical care should supply Filipinos with vaccinations and medicine for diseases such as tetanus, measles, rabies, hypertension, tuberculosis, and other NCD’s. However, difficulties in distributing them from Cuyo Island to the other isles preclude their availability elsewhere in the archipelago. There is a need for a design that improves upon the distribution system in place in the Cuyo Archipelago, and other similar island clusters.
To solve this problem, we’re creating an autonomous battery-electric catamaran, capable of carrying 20 kg of medical cargo for at least 30 km. The vessel will operate without the need for human intervention during operation. Our design will be easy-to-deploy, reliable, and affordable. Our long-term vision is to create a fleet of similar vehicles to service these archipelagos.
Design Considerations
Our design will have a range of 30 kilometers at a speed of 3 m/s, which is comparable to current boats in the region. Launching from Cuyo, our design will reach Agutaya, the second biggest island in the archipelago, in just under three hours, as well as many smaller islands in the area (see Figure 3). With two launching points, Cuyo and Agutaya, a boat with a 30 kilometer range could reach every island in the archipelago (Figure 3). In addition, our design will be capable of traveling significantly farther at lower speeds as the power it expends to overcome drag is proportional to the cube of its velocity.
Figure 3: Diagram of reachable islands for 30 km and 70 km ranges.
An estimate for the payload of our design comprises of a weekly demand for medical supplies of the outlying islands of the archipelago. Dr. Sampang-Abiad, a doctor who collaborates with WeRobotics and who has worked extensively in the Philippines, specifically in the Cuyo Archipelago, recommended medicines for common medical situations encountered in there, including vaccines for rabies, measles and tetanus, Oxytocin, and various medications for certain non communicable diseases (NCDs). Weekly demands were derived from yearly incidence rates reported by public health reporting bodies in the Philippines. The payload demands for the medicines, and for the storage container necessary to maintain the temperature of the medicines, can be found in Table 1. Thus, our design must be able to transport approximately 20 kg.
Table 1: Total estimated weekly mass.
Analyzing the local conditions in the Cuyo Archipelago, we also found that our design must remain stable in wave angles up to 18° (around 2.75 m in height), and can traverse shallow depths, constraining our draft. This meant that we needed a relatively wide, shallow boat, with a draft of less than 20 cm. The high stability requirements, along with the need for a shallow draft in coastal waters, drove us determine that a catamaran is the optimal architecture for our vessel. To keep the vessel simple, and provide adequate control, we decided implement a two motor, differential thrust system. The lack of a rudder reduces complexity, while preserving maneuverability. The need for high reliability and low maintenance also drove our decision to use electric propulsion for the vessel.
Figure 4: Overhead view of catamaran with differential thrust.
Throughout the design process, we focused on maintaining the usability of our boat, as well as minimizing the cost. This boat will ideally be used by individuals with minimal training, and thus must be easy to maintain and deploy, and less expensive than the current existing solutions. In order to rent a boat for the day, the cost is USD 170, which is very expensive for locals. We aimed to make the cost of our boat USD 100 or less per trip. Furthermore, we aim to make a boat that can be easily deployable (i.e. the ability of the users of the boat to be able to load cargo and carry out the sequence to send the boat to a specified location) and maintainable (i.e. the ability of the users of the boat to be able to load cargo and carry out the sequence to send the boat to a specified location). This means aiming to make the boat as lightweight as possible and optimizing the storage compartment, as well as making most components able to be simply replaced.
Project Status
We’re currently working on finalizing the detailed design of our vessel and working on design analysis and validation. To validate our design, we’re conducting small scale testing in a flow pool and have developed a numerical stability model to verify the stability of our vessel. In addition, we are verifying our construction techniques by making a small scale version of a hull with our planned fiberglass construction method. Finally, we’re developing a dynamic simulator to test our planning and control algorithms. We are focusing on small scale currently, but plan to scale up all design validations in the coming months for the full scale model. We hope that we can begin testing our first full scale prototype by February.
Recent Articles
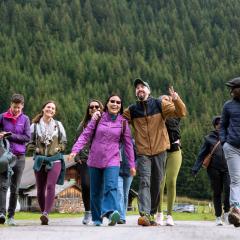
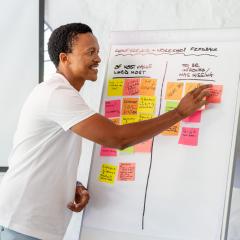